Notre céramiste en grès naturel
Antonio, le patron de cette belle petite unité de quarante personnes, nous a ouvert tout grand ses portes, pour une visite guidée autour d’un métier d’apparence rudimentaire, mais où savoir-faire très pointu et tour de main bien ajusté sont exigés à chaque instant. De fait, chez tout (bon) céramiste, il y a très peu de turn-over des effectifs, car le capital de l’entreprise, c’est l’expérience de chacun de ses employés, acquise année après année, et transmise « sur le tas ».
La préparation de la matière première:
Il en va du grès comme du pain: la recette de base de la pâte est élémentaire, mais au final, il en existe une infinité de variantes. Pour le grès, toujours du feldspath, du kaolin, du sable et de l’argile, mais qui seront dosés un peu différemment d’une entreprise à l’autre. Ajoutons à celà que chacun de ces composants n’est jamais 100% pur et/ou rigoureusement identique selon sa provenance. Chaque « terroir » apportera ainsi ses nuances. Par exemple, d’une région à l’autre, on trouvera des argiles plutôt rouges (contenant du fer), d’autres seront grises (carbonées), ou blanches (calcaires). Chaque céramiste travaille donc un mélange qui lui est propre, qu’il maitrise bien (en cuisson notemment) , et auquel il restera fidèle sous peine de perdre ses repères. Certains les achètent tout faits auprès de grossistes, d’autres, c’est le cas d’Antonio, préfèrent le préparer eux-mêmes à partir de minéraux bruts, sourcés localement.
Alors, c’est parti pour un tour, et attention à la poussière…!!
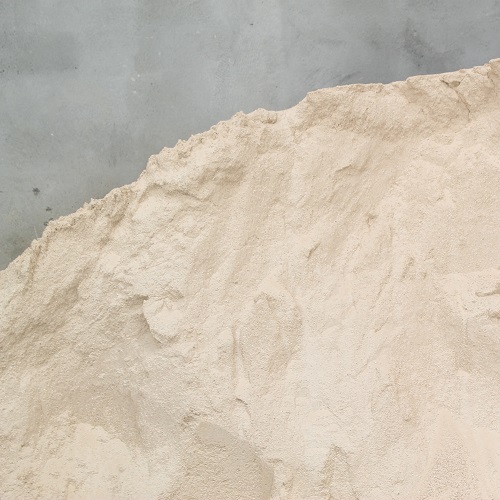
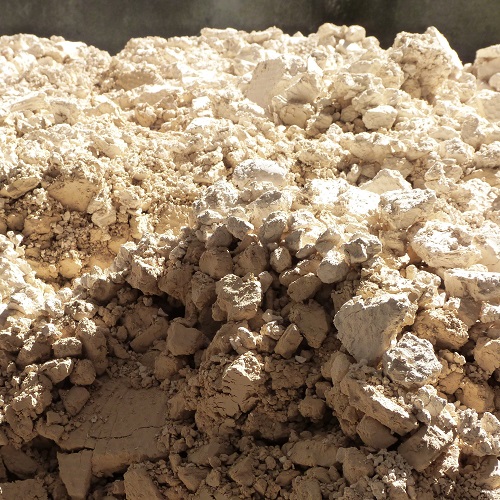
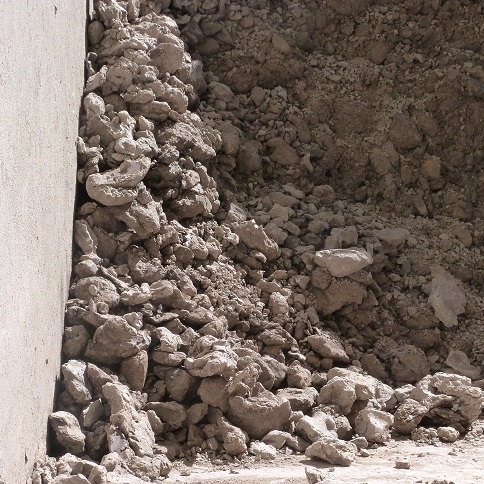
Feldspath…
Kaolin…..
Argile grise…..
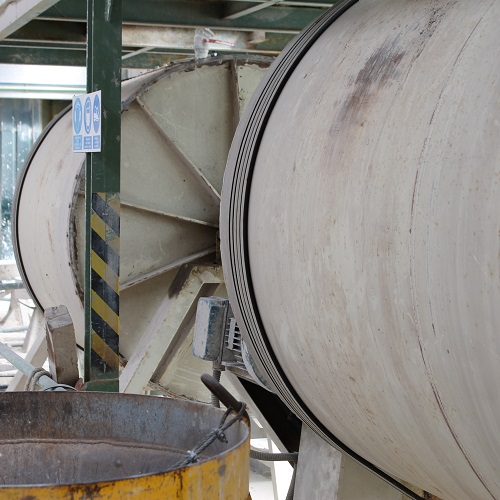
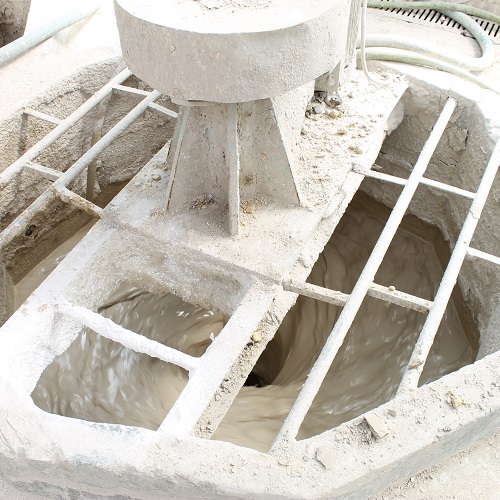
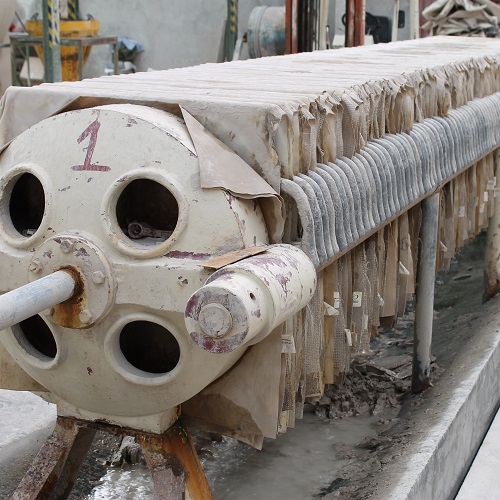
Une concasseuse à galets réduit le mélange en fine poudre…
qui sera ensuite diluée et mixée en une pâte liquide, la barbotine….
elle-même égouttée dans cette presse géante.
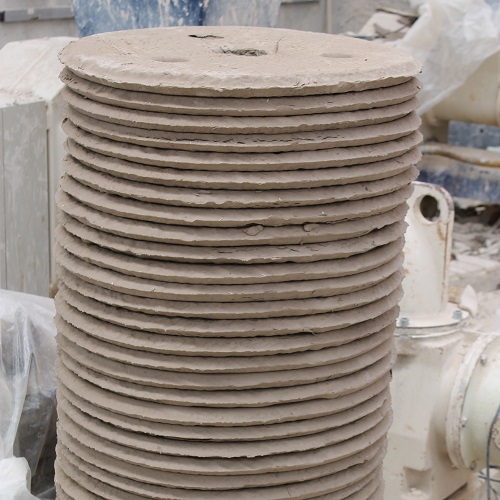
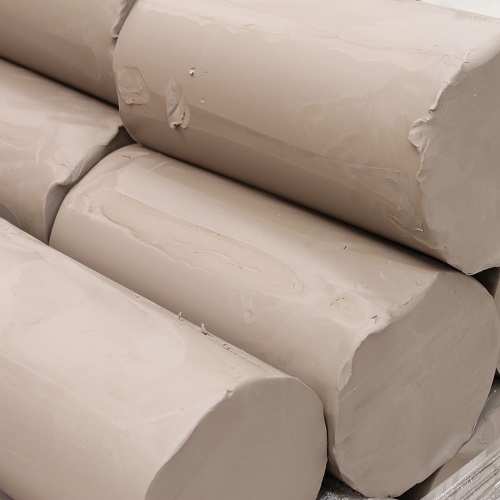
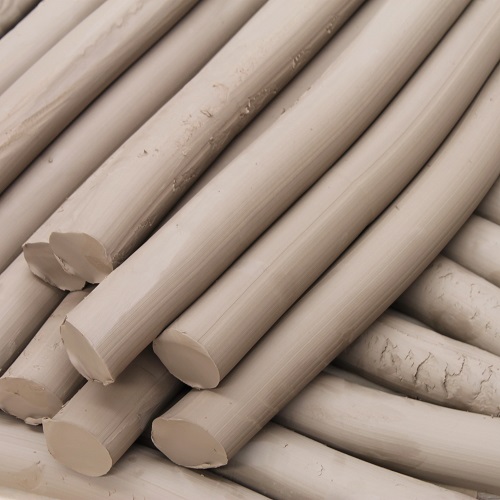
On en retire ces disques de pâte qui seront ensuite malaxés
et extrudés sous forme de blocs de gros diamètre
ou de fin diamètre.
Le façonnage des pièces:
A ce stade, la matière se présente soit sous forme de barbotine, un mélange liquide ayant la consistance d’une pâte à crèpes, soit sous forme de blocs de matière ressemblant à de la pâte à modeler.
3 techniques de façonnage seront alors utilisées:
– le moulage à la presse, pour les pièces plates et de grande taille (assiettes, plats)
– le moulage au tour, pour les pièces circulaires et de taille moyenne ou hautes et évasées (bols, petits récipients)
– le coulage, pour des pièces complexes (pichets avec des anses, vases avec des cols étroits, etc…). Cette technique permet l’élaboration d’une pièce d’un seul tenant, sans collage, ni aucun assemblage.
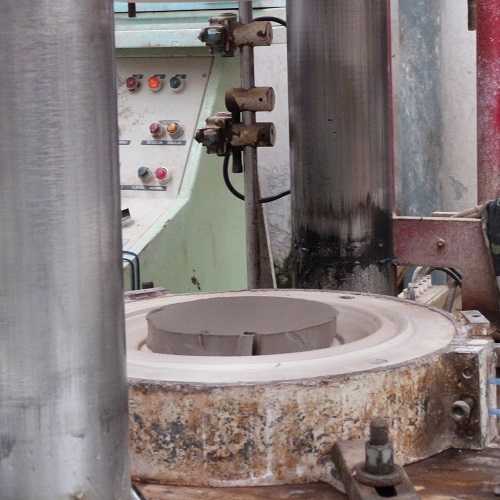
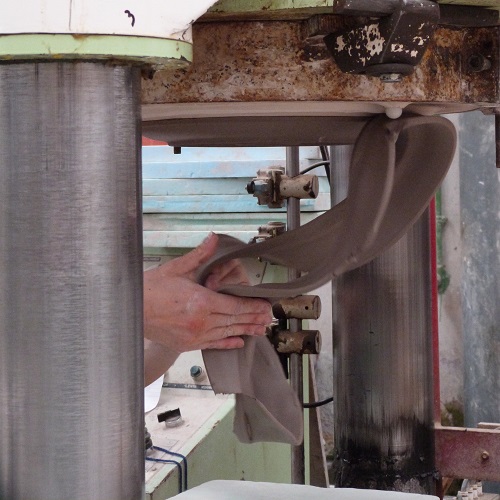
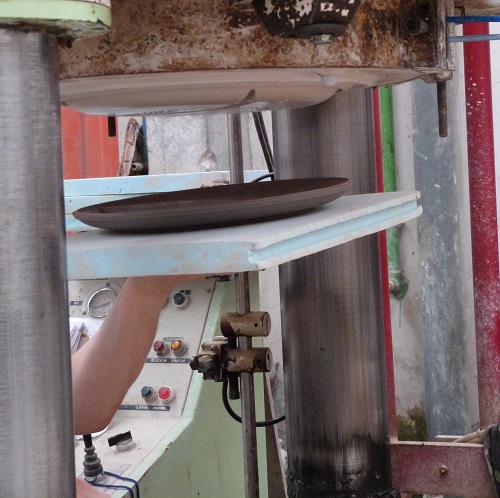
A la presse: on dépose un « camembert » de grès sur le moule
La presse monte sur le contre-moule et imprime sa forme à l’assiette…
Après avoir retiré ce qui à débordé sur les côtés, on démoule…
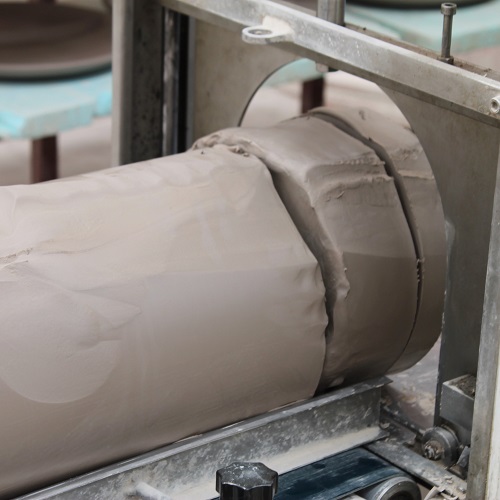
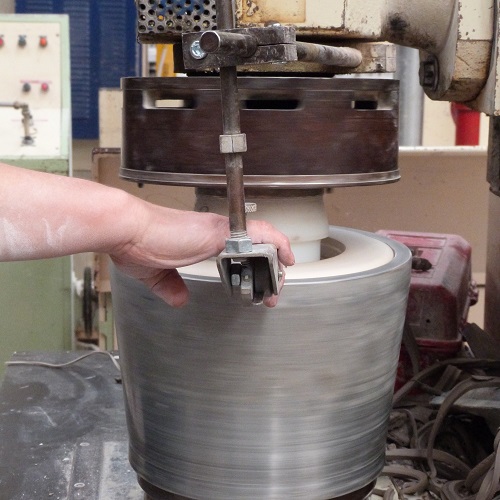
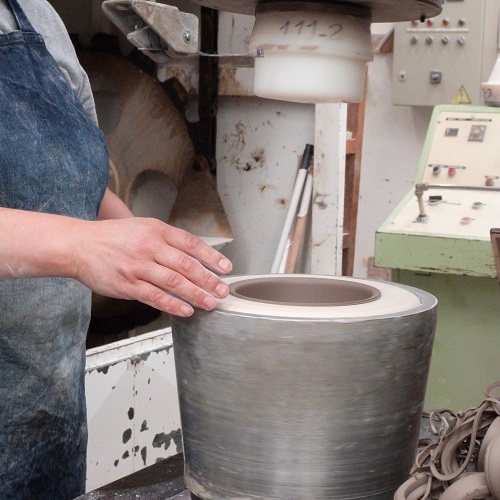
Au tour: on commence pareil, un « camembert »…
petite différence ici, la base tourne et le contre-moule descend…
on enlève le surplus et il ne reste plus qu’à démouler.
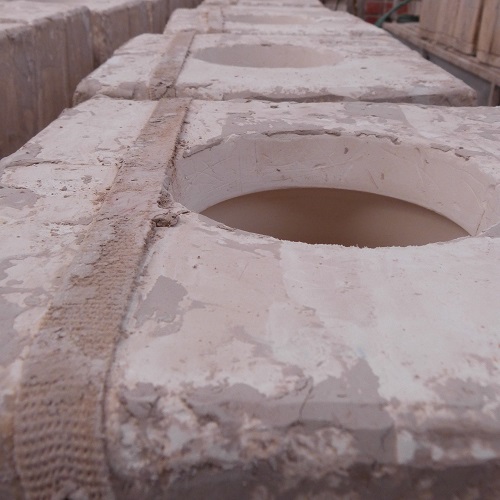
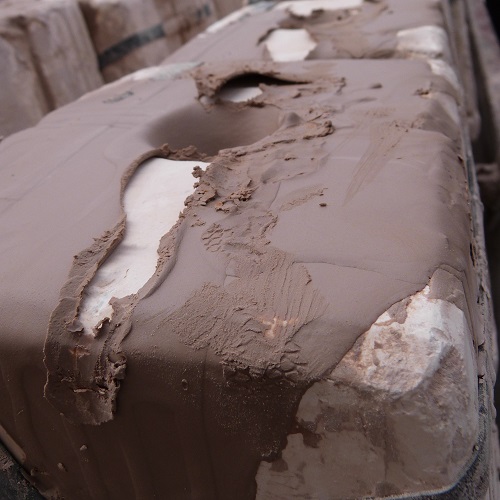
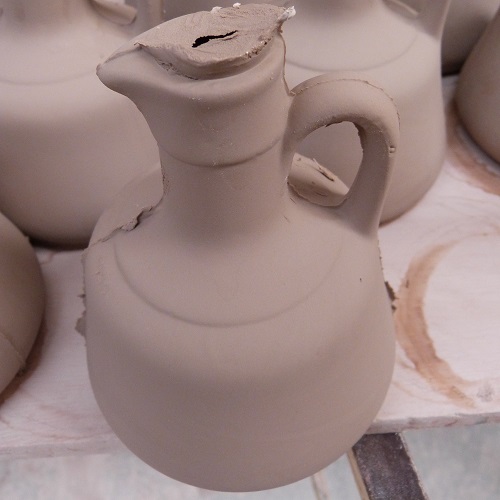
Au coulage: deux 1/2 moules en plâtre, sanglés l’un contre l’autre…
remplis de barbotine, qui séchera sur quelques mm au contact du plâtre…
on vide l’excédent resté liquide à l’intérieur, on démoule, magique….!
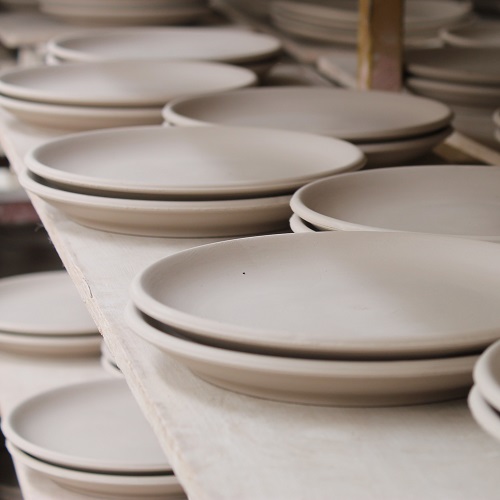
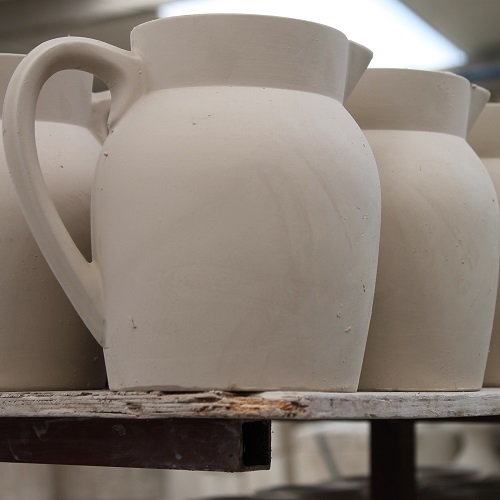
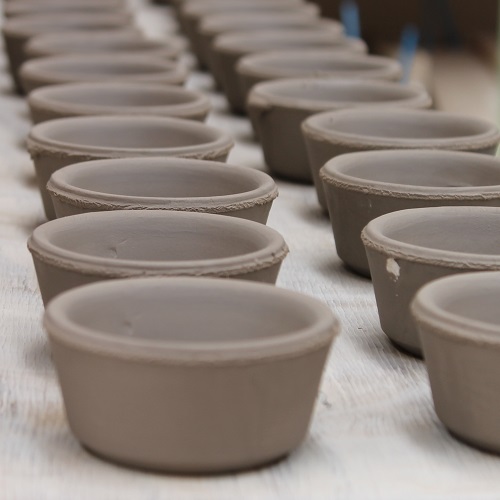
Etape importante avant émaillage…
retouches et finitions à la main…
passage au séchoir (chaleur récupérée des fours de cuisson).
Emaillage et cuisson:
L’émail est un mélange liquide que l’on dépose en superficie de la céramique et qui va se vitrifier en changeant de couleur à la cuisson. Le « biscuit » de grès étant lui même intrinsèquement étanche, l’émaillage n’a ici qu’une fonction décorative (couleurs) et d’aspect (toucher lisse).
La pâte et l’émail ne cuisent pas à la même température. En principe, on cuit donc d’abord la poterie crue de grès, le « biscuit », avec des montées en température bien spécifiques, on laisse refroidir, on émaille, et re-belote, mais avec des courbes de chaleur différentes, pour bien cuire l’émail cette fois. Simple, imparable, mais long et très gourmand en énergie (2 cuissons).
Antonio utilise plutôt la technique moderne de la mono-cuisson. En établissant un timing bien précis de montées en températures, de paliers minutés et de refroidissements également parfaitement sous contrôle, on parvient à faire les deux en même temps. Des fours modernes au gaz, pilotés par ordinateur, très souples, et bien isolés sont ici nécessaires. Très chers à l’achat, mais il n’y a ici qu’une seule cuisson. La chaleur résiduelle sera en plus recyclée pour alimenter les séchoirs (voir ci-dessus).
Petite anecdote: la couleur de l’émail liquide n’a rien à voir avec la couleur finale. Le bac d’ émail rose « malabar » que vous voyez ci-dessous est celui utilisé pour notre couleur « grès naturel », plutôt blanc-crême granité au final…
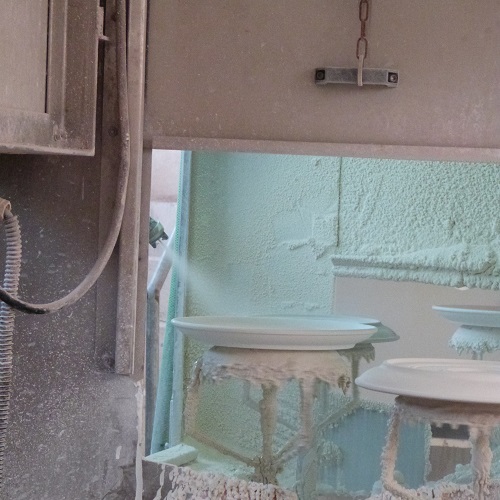
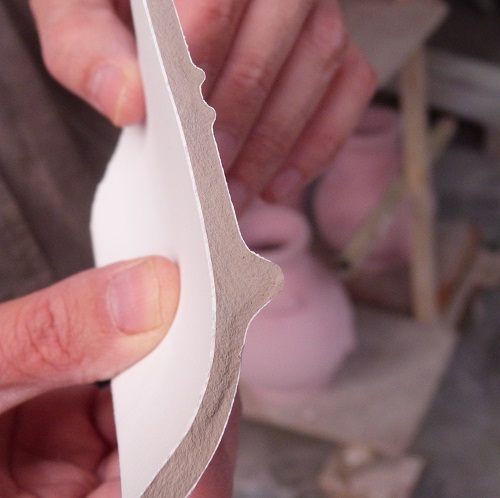
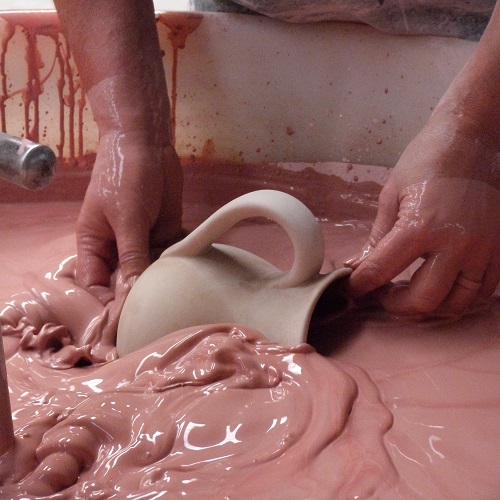
Emaillage par pulvérisation
L’émail se dépose en très fine couche
Emaillage au trempé
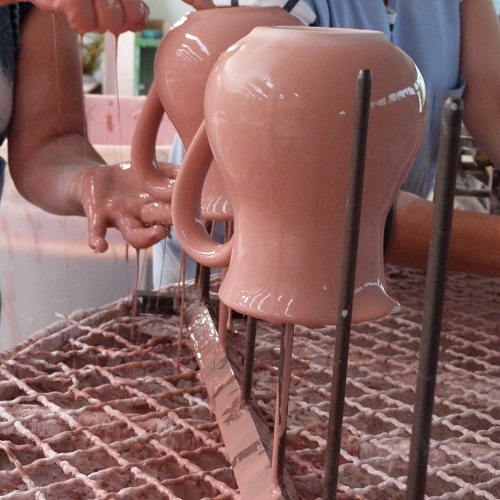
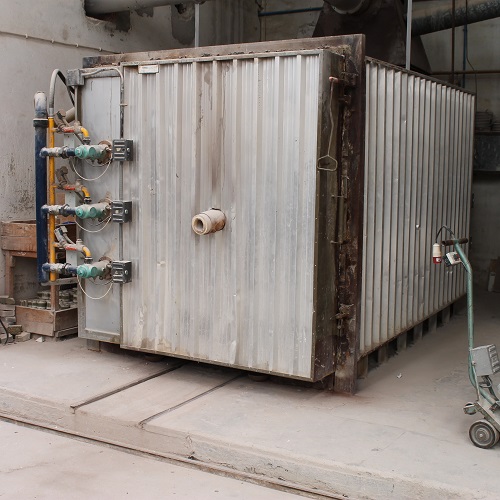
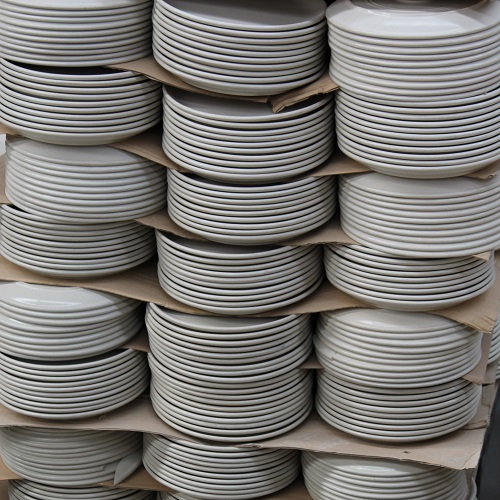
Egouttoir
Cuisson au four (plusieurs heures)
Stockage, emballage, expédition…
Bonus:
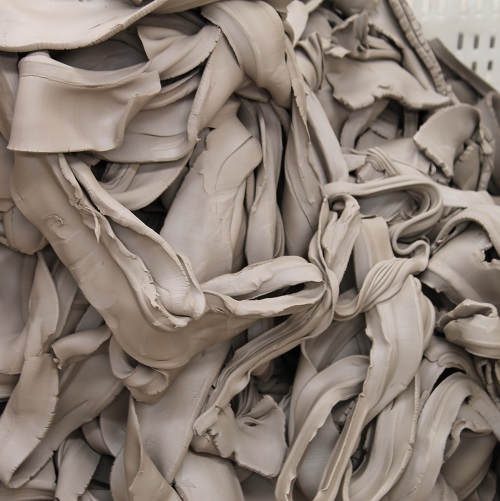
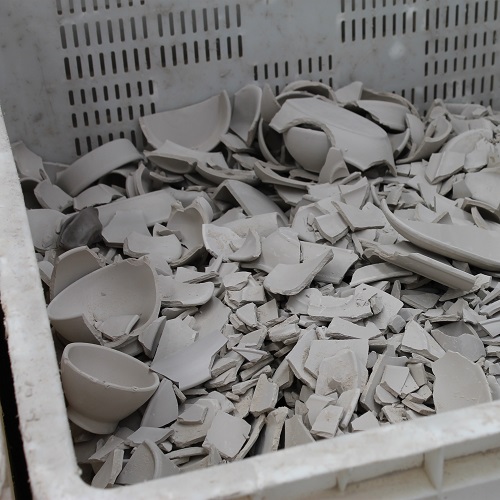
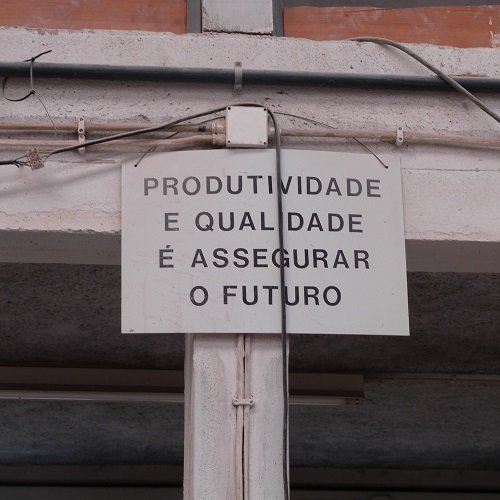
Les chutes de moulage seront recyclées dans la barbotine…
Errare humanum est! Les débris seront broyés et réincorporés dans le mélange initial eux aussi…
Slogans productivistes et empirisme du cablage cohabitent à merveille: la taille humaine comme on l’aime !